
- Improving casting quality: the advantages of bauxite
- The high-temperature charm of bauxite for refractory sand
- Bauxite: High-temperature protection for welding rods
- Bauxite: the secret weapon of cast iron coatings
- Bauxite: The core component of refractory castables
- Improve casting quality, the secret of bauxite
- Bauxite promotes technological innovation in lost foam casting
- Bauxite for blast furnace smelting: Selection criteria revealed
- Bauxite: the key material for lost foam casting
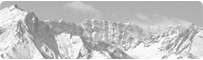
processing of bauxite
Bauxite is usually strip mined because it is almost always found near the surface of the terrain, with little or no overburden. As of 2010, approximately 70% to 80% of the world’s dry bauxite production is processed first into alumina and then into aluminium by electrolysis. Bauxite rocks are typically classified according to their intended commercial application: metallurgical, abrasive, cement, chemical, and refractory.
Usually, bauxite ore is heated in a pressure vessel along with a sodium hydroxide solution at a temperature of 150 to 200 °C. At these temperatures, the aluminium is dissolved as sodium aluminate. The aluminium compounds in the bauxite may be present as gibbsite(Al(OH)3), boehmite(AlOOH) or diaspore(AlOOH); the different forms of the aluminium component will dictate the extraction conditions. The undissolved waste, bauxite tailing, after the aluminium compounds are extracted contains iron oxides, silica, calcia, titania and some un-reacted alumina. After separation of the residue by filtering, pure gibbsite is precipitated when the liquid is cooled, and then seeded with fine-grained aluminium hydroxide. The gibbsite is usually converted into aluminium oxide, Al2O3, by heating in rotary kilns or fluid flash calciners to a temperature in excess of 1000℃. This aluminium oxide is dissolved at a temperature of about 960 °C (1,760 °F) in molten cryolite. Next, this molten substance can yield metallic aluminium by passing an electric current through it in the process of electrolysis, which is called the Hall–Héroult process, named after its American and French discoverers.
Prior to the invention of this process, and prior to the Deville process, aluminium ore was refined by heating ore along with elemental sodium or potassium in a vacuum. The method was complicated and consumed materials that were themselves expensive at that time. This made early elemental aluminium more expensive than gold.
The prev one: The global market of calcined bauxite
The next one: Stronger RMB supports bauxite prices
24-HOUR SERVICE, SPECIALLY FOR YOU
Email: info@sinocean.ltd
Tel: +86-371-55970121
Fax:+86-+86-371-66684099